Welcome to the Backyard
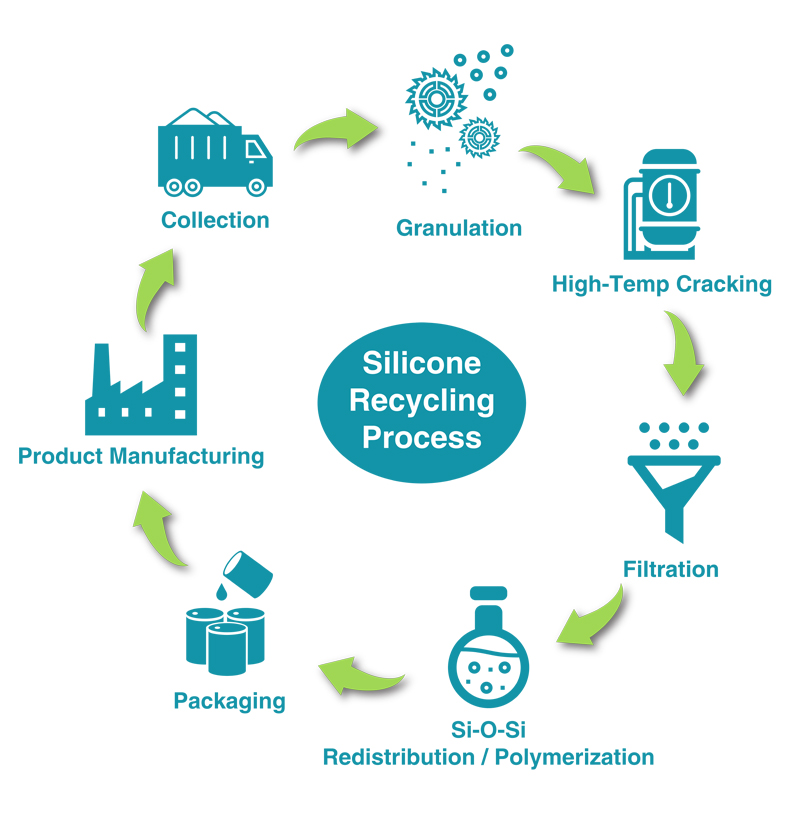
The “backyard” is where we recycle the silicone rubber that comes into our recycling facility. Unlike plastic, paper, or glass recycling that is straight forward, recycling silicone rubber is relatively complicated. Our silicone recycling process chemically breaks down silicone rubber, a solid, and processes it into silicone oil, a liquid. Silicone oil (PDMS) is the building block for manufacturing a variety of silicone related products. See our step-by-step silicone recycling guide below.
– STEP 1 –
Collect Silicone Rubber Worldwide
The silicone recycling process starts with the worldwide collection of our feed material, silicone rubber. The silicone rubber we collect are primarily from manufacturers of silicone products such as pacifiers and baby bottles, medical tubing and parts, automotive parts such as wire harnesses, silicone mats and boards, and more. The silicone rubber material we collect are often reject goods, “cut offs”, “runners”, and leftover materials.
We also process expired, used, or surplus silicone oil (PDMS) in liquid form. For example, do you have the following materials?
Dow Corning XIAMETER™ PMX-200
Wacker AK Series PDMS
Momentive ELEMENT 14
Shinetsu KF Series PDMS
*We welcome other brands and models.
In addition to PDMS, we also collect expired and surplus liquid silicone rubber (LSR), silicone sealant (RTV), and other liquid materials related to silicone.
If you have any of these materials, contact us to for a free consultation. Make sure to ask us about our free pick up services and plant analysis.
– STEP 2 –
Granulate into Small Pieces
We guarantee the secure destruction of all silicone rubber we collect. After collection, the silicone rubber is sorted and ground into small pieces. This process helps the silicone rubber to heat evenly in the next step.
Learn more about secure destruction.
– STEP 3 –
High Temperature Cracking
The next step of the silicone recycling process involves a chemical cracking process whereby the collected silicone rubber is heated in a large chemical reactor. This process chemically breaks down the silicone rubber and takes several hours to complete. The vapors from the reactor are cooled and collected through a complex array of apparatuses. The resulting liquid is composed of a mixture of the fundamental building blocks required to make silicone oil.
– STEP 4 –
Filtration
The liquid collected in the above step is a precursor to producing PDMS silicone oil. The technical term for this liquid is dimethylcyclosiloxane. At this stage, the liquid is in a raw form and filled with impurities. The liquid that has been collected so far goes through a series filtration to remove solid impurities.
– STEP 5 –
Redistribution
The filtered liquid dimethylcyclosiloxane (DMC) is now ready for a “redistribution” process to further breakdown the chemical structures of the Si-O-Si bonds and to remove and excess moisture and impurities. The outcome is pure DMC that is clear, odorless, and water-like. This is the basic building block for producing our final product, silicone oil or polydimethylsiloxane (PDMS).